Projektinitiativ #59: 3D analysis of component performance ( 3 kommentar)
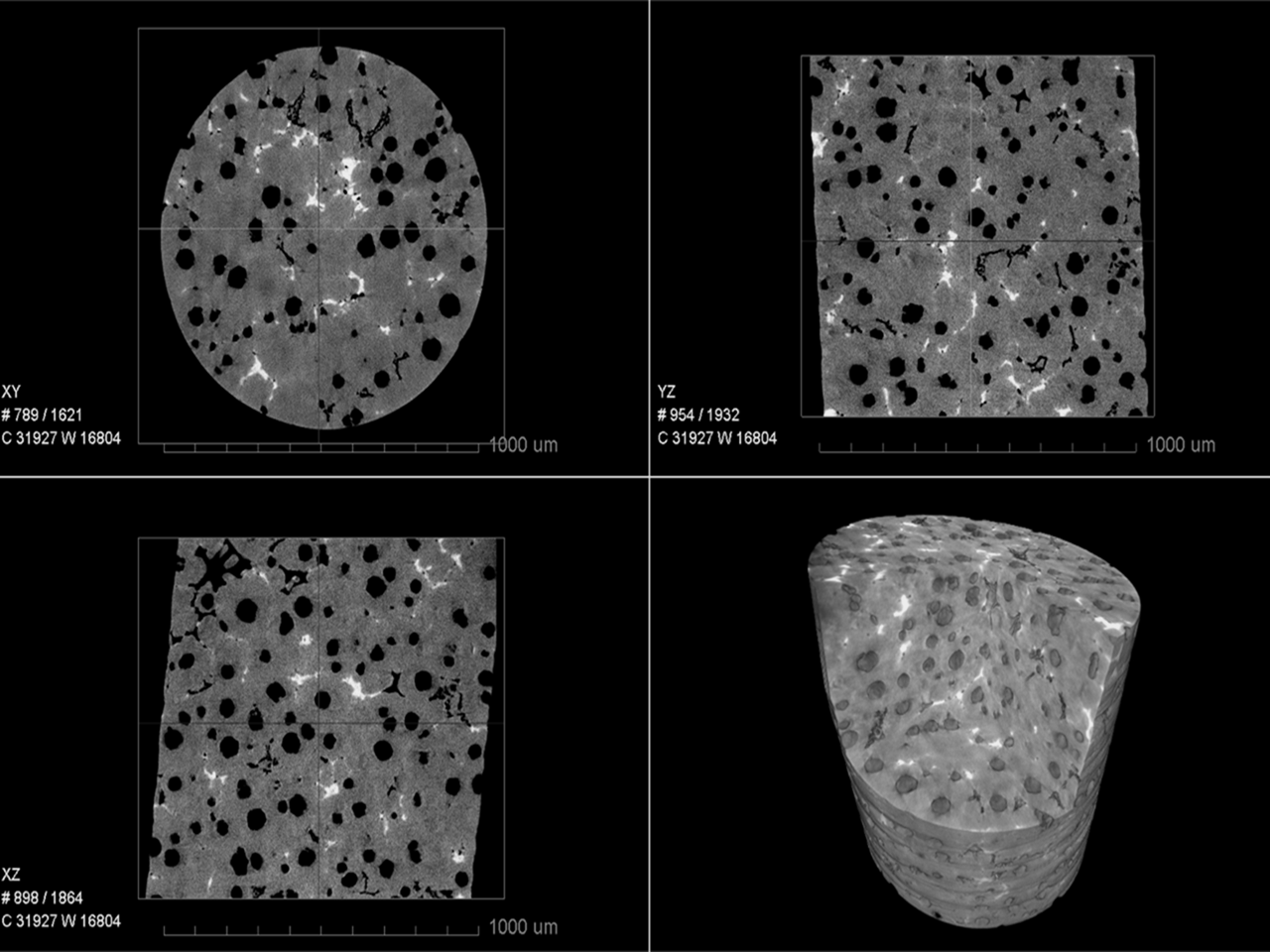
The increasing demand for high performance cast iron components in applications e.g. requiring increased combustion pressures to safeguard reduced emissions in combustion engines, gives rise to increased thermal and mechanical loads. High performance components are realized by an improved understanding of the active damage and deformation mechanisms.
Therefore, characterization of the graphite and the matrix microstructure is needed in Swedish foundry industry to ensure component performance. The common way to do this characterization is to take a sample and analyze it in two dimensions. There are clear limitations to this as local variations are often present in cast materials. Furthermore, even if static testing, fatigue testing and thermo-mechanical testing promote some understanding of the damage and deformation mechanisms, deeper understanding is only possible for in situ analyzes in three dimensions. This can be accomplished using tomography methods.
The basic approach of this project initiative is to investigate whether it is possible to quickly describe the material microstructures in three dimensions in order to get a far safer description. The uniqueness of this effort is to investigate various concepts for time effective characterization of the microstructure in cast iron (grey, ductile and compacted) in three dimensions. Here 3D information for the quantification of pore and graphite fraction of the cast irons will be compared with classical microscopy 2D data. Additionally, the potential for in-situ tomography of damage and deformation mechanisms to elucidate the grain structure and the elastic strains of individual grains will be considered. It is envisioned that correlating observations at different length scales can achieve a deeper understanding of the material properties.
For the analysis of strains in the interior of the materials full-field methods, like digital volume correlation (DVC), can be used based on the volume images. For future larger research projects, the viability of utilizing synchrotron light available at MAX IV in Lund will be investigated for applications requiring improved spatial and temporal resolution of the 3D analyses.
The presented initiative is important for the competitiveness of Swedish automotive and foundry industries. Since the methods used in the feasibility study are generic the results of the project ought to be of interest for e.g. the steel industry and additive manufactured materials.
Namn Torsten Sjögren
Organisation RISE Research Institutes of Sweden
Kommentar #1
Advanced 3D characterization techniques can provide deeper understanding of material properties, and may thereby lead to higher component performance levels. From a more extensive knowledge of cast materials, we may also define a set of key material parameters that could be monitored and enable the development of more relevant on-line methods for quality control.
A possible further extension of the proposed project initiative would therefore be to relate the knowledge of cast materials obtained from the proposed 3D characterization studies to more relevant on-line measurement techniques for quality control.
Namn Bertrand Noharet
Organisation Swerea KIMAB
Kommentar #2
A very important initiative to increase the understanding of cast iron microstructures, and how they influence the final properties. We know that 2D not is enough to fully understand the behavior and therefore 3D and DVC is a very interesting approach. The influence of defects on the mechanical properties is also interesting, as well as defect detection and quality.
Namn Lennart Elmquist
Organisation Swerea SWECAST
Kommentar #3
Full 3D-analysis of the microstructure of cast irons, including graphite classification, identification of defects and pores as well as the possibility to monitoring crack growth are very interesting for companies such as Scania.
First it could replace or complement the time consuming and partly subjective 2D-analysis done using classical microscopy. Today conventional 2D microscopy in connection with analysis software is used to characterize cast irons on a daily basis in companies such as Scania and the following classification of the irons are done according to relevant ISO-standards. The process is however time consuming and to some extent also subjective and dependent on the choice of measuring spots done by the metallurgist. Further, usually a single 2D slice of the specimen is analysed and used to characterize the entire specimen giving large uncertainties regarding the microstructure of the rest of the specimen where different solidification and cooling rates may give large differences in the microstructure. The possibility to use 3D scanning computed tomography and full field analysis methods such as DVD (Digital Volume Correlation) would eliminate the drawbacks with the 2D- characterization methods used today. Instead a 3D analysis would give a much more objective and correct characterization of the structure of the specimen.
Secondly it could be used as an very important research tool when analysing damage and crack propagation in different types of fatigue problems. The possibility to reveal the growth of microcracks and the changes of the microstructure during different stages of the fatigue process would enhance the knowledge and improve our possibilities to design more durable components.
Namn Jessica Elfsberg
Organisation Scania CV AB