Projektinitiativ #95: A framework for the physics-based estimation of tool wear in machining process
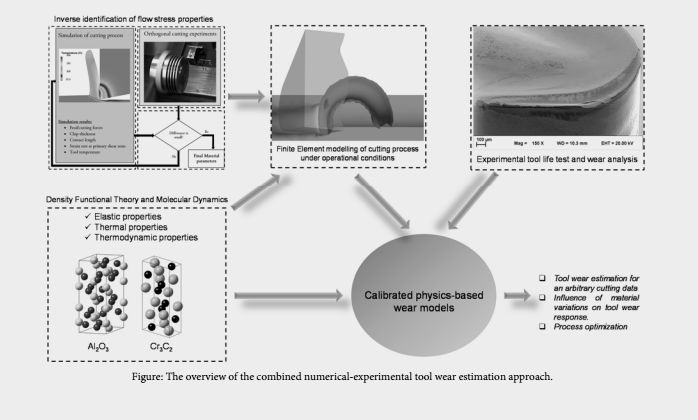
Metal cutting process is often regarded as the final step in production of industrial components, at which the parts are closely dimensioned, new features like holes, chamfers and fillets are made and the specific demands on the properties of machined surfaces are secured.
Lars Nyborg presents the initiative during the 2017 conference
In cutting process, the tool edge is normally subjected to the large thermo-mechanical loads, the levels of which may respectively exceed to 5 GPa and 1100 °C depending on the severity of the cutting data and physical properties of tool and work material. As a result, the tool edge may gradually wear down during the cutting process, or it may undergo abrupt failure under extreme conditions. The worn geometry of the cutting edge may in turn deteriorate the surface properties as well as the dimensional accuracy of the machined parts. An accurate estimation of the tool wear development is therefore of utmost importance for the optimum machining in terms of cost and time, while secu ring the requirements on the functional surfaces. The conventional methods for tool life estimations are often based solely upon a large number of costly experimental tests. An alternative solution would be utilising the calibrated physics-based models to reduce the number of experimental tests from one hand, and to provide a framework to evaluate the tool wear response due to material variations on the other hand, for example the effects of variations in the amount of abrasive particles or solid solution elements on tool wear responses. A combined numerical- experimental approach may therefore provide a sustainable solution for process optimisation and prediction of tool wear behaviour.
Computational techniques based on solid-state and molecular physics can effectively be applied to derive a wide variety of thermodynamic and mechanical parameters required in engineering models, such as thermal expansion coefficients and elastic constants. A crucial requirement is to define robust interfaces between their outputs and the inputs of computational models developed for structural design applications and typically based on continuum mechanics. In this proposal, we intend to support the development of physics-based wear models for machining applications. An assessment of the existing strategies to link microscopic calculations and empirical models used in industrial practice will be performed, together with a systematic mapping and quantification of the various sources of numerical and physical approximations that contribute to the uncertainty of the final output.
Namn Amir Malakizadi
Organisation Chalmers University of Technology